5 reasons printed circuit boards fail – and how to avoid them
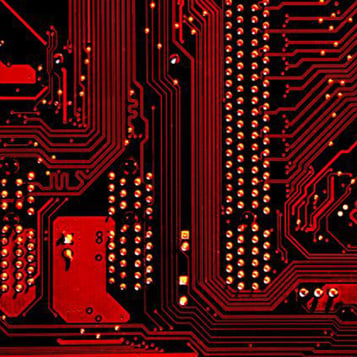
PCB failure is frustrating. It’s costly, inconvenient and can negatively affect your brand. Printed circuit boards are sensitive things though, and failures can be caused by a number of things – from the weather to age. Here are the top five reasons that printed circuit boards fail, and how you can reduce the risk of failure.
1. Environmental factors
PCBs in damp or particularly hostile environments are prone to these types of failure because, as temperatures change, the PCB can expand and contract and boards may become warped. With all this movement it’s easy for soldered joints to become damaged, leading to board failure. This sort of issue is most likely to be seen when a component’s barrier has been broken and atmospheric particles such as dirt, dust and moisture get into the component, or circuit board.
2. Poorly manufactured components.
One of the most common reasons for failure is a poorly manufactured PCB. Issues such as incorrect soldering temperatures, misalignment of the bare board & components and dry joints all indicatives of a poorly manufactured PCB.
When looking for a PCB manufacturer, find one that has been around a while, with a good reputation. The business world has a beautiful way of casting off the poor manufacturers over time.
3. Burnt components
Printed circuit boards can get pretty warm, and in doing so components work outside their standard operating temperatures. The amount of heat that a component can take is finite and depends largely on its size and structure. Make sure that when designing your PCB your components have sufficient space around them to allow air to circulate around any heat sinks, and they will be working within their operational capability.
4. Electrical overloading
Overloading a printed circuit board with excessive current or voltage can lead to component failure and board damage. This can occur due to power surges, short circuits, or incorrect power supply specifications. To avoid electrical overloading, ensure the PCB design and component selection are compatible with the intended power requirements. Implement protective measures such as fuses, voltage regulators, and surge protectors to safeguard against overloading and prevent catastrophic failures.
5. Contamination during assembly
Contamination during the assembly process can cause short circuits, corrosion, and other issues that lead to PCB failure. Contaminants such as flux residues, solder splatter, dust, and debris can compromise the integrity of solder joints and electrical connections. To minimise the risk of contamination, follow strict cleanliness protocols during PCB assembly, including thoroughly cleaning components, equipment, and workspaces. Use high-quality soldering materials and fluxes that leave minimal residues, and implement proper handling procedures to prevent contamination from human contact.
In conclusion, while printed circuit board failures can be frustrating and costly, they are often preventable with proper care and attention to detail. By addressing common causes of PCB failures mentioned above, we stay aware to reduce the risk of failures and improve the reliability of their electronic devices.
Remember, choosing a reputable PCB manufacturer with a track record of quality and reliability is essential for minimising the risk of failures and ensuring the success of your electronic products. Ready to ensure the reliability of your PCBs? Contact us today to discuss your PCB manufacturing needs and learn how we can help you avoid common pitfalls and deliver high-quality, dependable products.