Our PCB customer service – Keeping lead times low, even for more unconventional materials
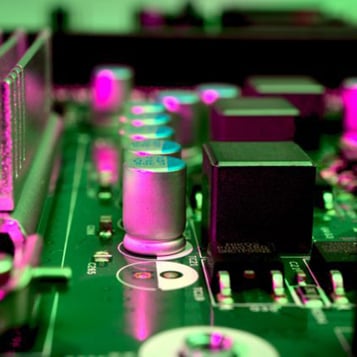
Our PCB customer service – Keeping lead times low, even for more unconventional materials
We work with so many different types of organisations and industries, each unique, and with so many diverse uses for our PCBs, it’s inevitable that, in some situations there’s a lot riding on their reliability and with that our excellent PCB customer service.
Our experienced PCB customer service regularly work with security and surveillance organisations. Where, as well as needing to be reliable and dependable, PCBs must be able to operate in hostile environments, where temperatures and air pressure can fluctuate vastly in short spaces of time, and units are assaulted with sand, wind and rain on a regular basis.
Components built to deal with these kinds of conditions can be hard to get hold of. Low demand and specialist hand-manufacturing mean that lead times, and delivery times, can be extensive.
TMM 6 and TMM 10 boards are composite boards hand-made for aeronautical use. Built in the States, they are designed to cope with high temperatures on the ground, and temperatures that do more than ‘dip’ below freezing in the air.
Lead times for these components can be as long as 10-16 weeks, and when you add design, printing and build time, the total delivery time from placing an order to receiving delivery of these robust PCBs to a client could be as long as 5 months.
We know that when expensive missions, and even lives, are dependent on the reliability of these tiny but clever components, that kind of a wait just doesn’t cut it.
In conclusion, our commitment to exceptional PCB customer service extends beyond traditional lead times, even for unconventional materials. We understand the critical importance of reliability, especially in high-stakes environments like security and aerospace. That's why we prioritise efficiency and responsiveness to ensure timely delivery, no matter the complexity or rarity of the materials involved.