Hold tight for a surge in rigid-flex board demand
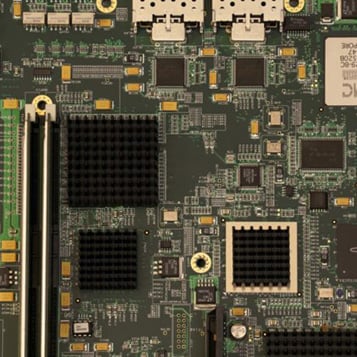
Rigid-flex boards are enjoying a surge in popularity right now. Wearable tech and the Internet of Things has driven the demand for rigid-flex boards to new, heady heights.
Market experts are predicting a further surge in demand for rigid-flex boards as products and designs adapt to take advantage of new technology and evolving consumer demands.
A survey published last year by Lucintel predicted that the next few years are likely to bring about the highest growth in demand yet. This growth is expected to be driven by the increased demand for smartphone and display applications.
Wearable tech is just one area in which boards are being used and it’s expected that this industry alone is set to grow to $30.6 billion by 2020.
Contrary to public belief rigid-flex boards have been used in the military and aerospace industries for over 20 years.
Giving you the option to fold your circuitry into almost origami-style into rectangles, cubes, or octahedrons, circuit boards can be made to fit the design of your product. This up-ends the traditional approach of designing a product around essential circuity and allows product designers and brands more freedom and flexibility.
What are rigid-flex boards?
Typically a rigid-flex board is made up of a number of flexible circuit inner layers, attached together using an epoxy pre-preg bonding film. They require a rigid board, connected either internally or externally through plated thru holes to deliver additional support where it’s needed.
Then the flexible sections of the board enable the circuit board to follow corners and accommodate parts that need more space.
The most common rigid-flex combinations
The most common rigid-flex combinations are 4 layer rigid-flex, 6 layer rigid-flex and 8 layer rigid-flex but there are a vast number of combinations available, each offering their own benefits. If you are considering using rigid-flex combinations within your prototype, it’s worth seeking specialist advice.
What are rigid-flex boards? Typically a rigid-flex board is made up of a number of flexible circuit inner layers, attached together using an epoxy pre-preg bonding film. They require a rigid board, connected either internally or externally through plated thru holes to deliver additional support where it’s needed.
Then the flexible sections of the board enable the circuit board to follow corners and accommodate parts that need more space.
most common rigid-flex combinations
The most common rigid-flex combinations are 4 layer rigid-flex, 6 layer rigid-flex and 8 layer rigid-flex but there are a vast number of combinations available, each offering their own benefits. If you are considering using rigid-flex combinations within your prototype, it’s worth seeking specialist advice.
Our team of engineers here at Garner Osborne will be able to advise you on the best combination for your design.