What you need to know before you choose flexible printed circuit boards
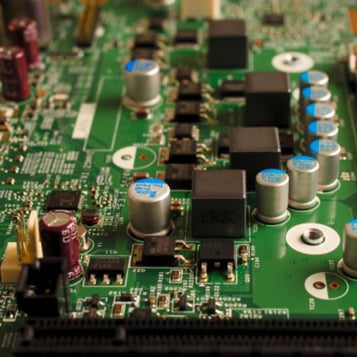
Flexible printed circuit boards (FPCs) are one of the fastest growing segments of the interconnection product market.
They enable product developers to finally break free of traditional restrictions on product design such as the shape, size and weight of the circuit board.
This level of flexibility is the reason why flexible printed circuit boards are finding their way into products in many industries, including aerospace and the military. They’re being used increasingly in mobile communications, laptop manufacture, and digital cameras too.
But, is the flexible circuit board really the answer to everything?
Flexible circuit board appeal
For the first time, designers of electronic products can allow product design, shape and size to be led by aesthetics or performance. Printed circuit boards can be rolled or folded, which means they can fit into a product of almost any shape or size.
Flexible printed circuit boards can also pave the way for additional product features, they can be used for high density device connection too.
With good thermal diffusivity and solderability, FPCs can work well and, if manufactured correctly, offer high reliability levels too.
Sounds almost too good to be true. Especially as the actual manufacturing process can be more straightforward.
However, during the manufacturing process, the circuit boards themselves are more fragile because of their mobility. This means it’s essential to use specialist FPC technicians for tin plating and rework in order to minimise the potential for poor connections and ultimately circuit failure.
Before you choose flexible printed circuit boards (FPCs) for your project, there are several key factors you need to consider to ensure success:
- Application requirements:
Evaluate your application's specific needs and determine if FPCs fit correctly. Consider factors such as flexibility, space constraints, and environmental conditions. FPCs are ideal for applications requiring lightweight, compact, and flexible designs but may only be suitable for some scenarios. - Design considerations:
Work closely with your design team to optimise the layout and configuration of FPCs. Consider factors such as bend radius, layer stack-up, and trace routing to ensure compatibility with your product's form factor and performance requirements. Proper design considerations are essential for maximising the benefits of FPCs and minimising potential issues during manufacturing and assembly. - Material selection:
Choose the suitable materials for your FPCs based on your application requirements and environmental conditions. We can also help you select materials with excellent flexibility, thermal stability, and reliability to ensure long-term performance. Conduct thorough research and consult with us to choose the appropriate materials for your project. - Reliability and Durability:
We prioritise reliability and durability when selecting flexible printed circuit boards for your project. We will also ensure that the chosen FPCs are created and manufactured to withstand the rigours of your application's operating environment, including temperature extremes, mechanical stress, and vibration. We will also pay attention to factors such as material quality, solder joint integrity, and resistance to environmental factors to maximise the longevity and performance of your FPCs. Investing in high-quality, durable FPCs can minimise the risk of failures and ensure the long-term reliability of your electronic products. - Quality assurance:
Apply robust quality assurance processes to verify the reliability and performance of your FPCs. We will also help you to conduct thorough testing and inspection steps to identify defects early in manufacturing. Prioritise quality and reliability to minimise the risk of failures and ensure customer satisfaction.
Thus, flexible printed circuit boards offer various benefits and opportunities for innovative product design. However, choosing the right FPC solution requires careful consideration of multiple factors, including application requirements, design considerations, material selection, manufacturing expertise, and quality assurance. By following these guidelines and working with experienced partners, you can harness the full potential of FPCs and create successful electronic products that meet the demands of today's dynamic market.
Ready to explore the possibilities of flexible printed circuit boards for your next project? Contact us today to discuss your requirements, and we can help you achieve your goals with high-quality, reliable FPC solutions.